Image
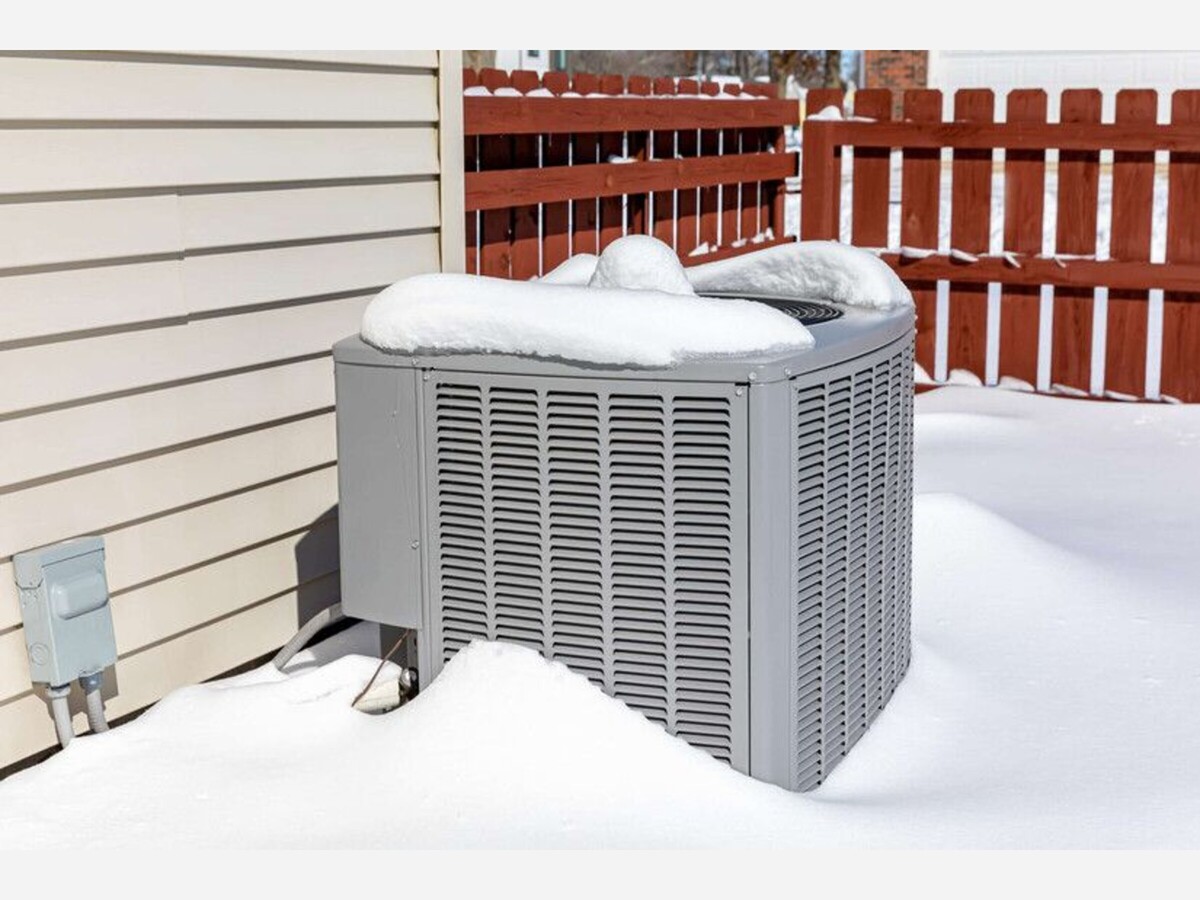
Winter is swiftly approaching. Soon, furnaces and heating systems will be running throughout the day and night to keep Hunt Valley area homes warm and safe. As temperatures drop, homeowners want to know, “How can I prepare my heating and cooling system for winter?”
Even as we anticipate a milder El Nino winter across this winter, local meteorologists are still staying alert for chilly temperatures and snowy events.
"During a strong El Nino as we are expecting this winter, colder air will remain bottled up to our north for longer periods of time while the moisture and storm tracks will remain south of us," say meteorologists."This doesn't mean we can't get stretches of colder temperatures. They will just be less frequest throughout the winter."
No matter how unpredictable our winter gets, make sure your furnace and heating equipment is prepared to efficiently heat your home this season when you take the right steps to maintain, test, and protect it. With good care and planning, keep your household warm with reliable heating equipment that performs well all winter long.
PIPCO AC shares the steps homeowners should take to ready their HVAC units for winter. You need to prepare your furnace for the cold and get your heating equipment ready. Find out what to do through the guide below – if you need professional help for heating repairs, maintenance, or system replacement, contact PIPCO today. They are the local experts for over 50 years.
Maintenance is the most important step to ensure efficient, reliable, and safe heating this winter. Contact PIPCO ideally in the fall. Furnaces and boilers should be serviced once per year, while heat pumps require service in the fall for heating and spring for cooling.
Air filters protect forced air HVAC systems from dirt, dust, and debris that cause inefficient performance and damage to delicate internal components. Air filters should be replaced on a regular basis, which can be anywhere from monthly to every 12 months, depending on the type of filter used – check the manufacturer’s information to determine the recommended replacement frequency for your filter.
If you haven’t changed your filter recently, get a fresh start for heating season and replace it now. During the winter, heating systems are in heavy use – it’s not unusual for filters to fill up faster and require more frequent replacement. Make it a point to inspect the filter monthly so you can tell if a new one is needed earlier than expected.
Operating a furnace or heat pump with a dirty filter this winter causes all sorts of issues you’ll want to avoid. When filters are dirty, they can’t do their job – more contaminants pass through into the furnace or air handler, where they can settle and accumulate on components, restricting their efficiency and causing damage. A filter that’s full of contaminants doesn’t allow proper airflow through the furnace or air handler, so the system consumes more energy as it works harder to move air – this can also cause equipment to overheat, leaving you without heat when the system shuts down for safety, and potentially damaging components which requires repair.
Many homeowners use whole-home humidifiers to replenish moisture that’s typically missing from winter air. This equipment is installed as part of your HVAC system and requires some maintenance each year.
Humidifiers keep relative humidity levels balanced in the home to alleviate dry air and the many issues that come with it. If the humidifier malfunctions, your home may not receive adequate moisture or receive too much moisture, leading to high humidity problems such as mold growth and water damage.
While a maintenance tune-up will clean out the interior chambers of the furnace or air handler, it’s a homeowner’s responsibility to keep the area around the furnace or heating system clean and clear.
Whenever it’s time to switch between heating and cooling modes, you want to make sure to change your programmed temperature settings, too! Household temperature preferences will differ for heating and cooling, and schedules may change seasonally, requiring setback periods to be adjusted.
Whether you have a heat pump or air conditioner, outdoor units need some care in the fall, too. Prep air conditioners for their off-season and get heat pumps ready to work this winter.
If your home is equipped with a boiler heating system that uses hot-water radiators, you need to bleed the valves on radiators prior to heating system. Bleeding the valves moves trapped air out to allow the system to heat rooms more efficiently.
A gurgling noise from radiators or banging sounds from pipes when the system runs tells you there is air in the lines and the radiators should be bled. Another sign of air in the pipes is if the radiator does not heat properly when the heating system is turned on. The top section of the radiator doesn’t get very warm, while the lower portion seems to be at the right temperature.
If you will be using a fireplace this winter, have the chimney inspected as you prepare to heat your home in the coming months. The National Fire Protection Association’s NFPA 211 standards indicate chimneys, fireplaces, and vents should be inspected annually at minimum to check for soundness, proper clearances and to ensure they are free from deposits.
The Chimney Safety Institute of America recommends that open masonry fireplaces be swept once they reach 1/8-inch of soot buildup, earlier if there is glaze in the system. Doing so eliminates fuel buildup to the volume where a chimney fire could cause chimney damage or spread into the home. For manufactured fireplaces, have the fireplace swept once buildup is noticeable, as deposits are acidic and can damage the integrity of materials.
Every home should be equipped with smoke detectors, and most need carbon monoxide detectors, too! Ensure this essential safety equipment is operational to keep your family protected throughout heating season.
For your furnace or heat pump to effectively and efficiently heat your home, all vents throughout your living spaces should be open and unobstructed. Closing vents to restrict heating is an energy-savings myth that actually leads to system damage. Your heating unit and ductwork are designed to deliver a precise volume of conditioned air to each area of the home – when a vent is closed or blocked, warm air is trapped in the system. This causes overheating, damage to ducts, and poor energy efficiency.
Before it’s time to turn on your heating system, make sure all vents in your home are open and uncovered.
Prior to the start of heating season, inspect your home’s HVAC ducts to ready the heating and cooling system for winter. Duct sealing eliminates the gaps, disconnections, and damage that causes heat loss and results in poor heating efficiency. You can inspect the ducts yourself or hire a professional to test for duct leakage and make repairs to the system to restore proper performance of your ducts.
Duct leaks are a major contributor to inefficient heating in the average Indianapolis home. Duct leaks resulting in 20% to 30% heat loss are fairly common. These air leaks are especially an issue in the winter, as a significant amount of heat is lost while circulating through ducts to your living areas – you lose this heat into unconditioned areas where it’s wasted instead of benefitting from it inside rooms.
Plus, cold air from the attic, crawlspace, or other unconditioned area where ducts run is able to get inside the duct system and move to living areas along with heated air, lowering the temperature of heated air arriving through supply vents. In turn, homeowners turn the thermostat up to generate more heat, so the furnace or heat pump does more work to make up for these losses.
You know which days of the year are typically the busiest for heating and cooling contractors? The first hot and first cold days of the year! On the first cold day of winter, many Indianapolis area homeowners are surprised when they go to turn on the heating system for the first time since spring – it doesn’t work. Stranded without any heat, emergency repairs are needed, and there’s a wait since numerous homeowners in the area face the same issue.
Avoid getting stuck in this situation by taking your furnace or heat pump for a test driver prior to the start of heating season. By firing up the heating system ahead of time, you’re able to verify its performance, ensuring that it comes on when it’s supposed to and heats your home to the desired temperature.
We recommend you do this a minimum of three times before we reach the point in the year where consistent heating is required in the home. Once or twice isn’t enough, and simply turning it on but not running a full heating cycle doesn’t cut it, either. There are plenty of mechanical issues that can exist while still allowing the furnace to turn on, yet heating performance isn’t where it should be. Or the system appears to run fine, but it’s on the verge of a breakdown.
As you test the performance of your furnace or heat pump before winter, don’t just assess what you feel – think about what you hear as well. Unusual furnace noises are indicators of system issues, which often result in diminished performance and the need for repairs.
Pay close attention to the noises you hear as the furnace or heat pump starts up, runs a heating cycle, and shuts down.
If your maintenance tune-up uncovers issues that require correction, or you know of performance problems that need to be addressed from the past season, it’s time to have those repairs made. Even if your furnace or heat pump is still operational, delaying repairs is likely costing you. System efficiency greatly declines, and you’ll experience difficulties heating your home this winter if you forego repairs. Further damage could be inflicted upon your HVAC equipment, creating the need for more expensive repairs later on – or even make replacement a necessity rather than a simple possibility.
Address all known heating repair needs prior to winter to avoid heating outages, inconvenience, and extra expenses. Scheduling repairs before heating season is in full swing means it’s more likely that a technician can get to you sooner. You won’t be stranded without heat when it’s freezing, generating the need for an emergency repair and the extra cost that comes with it.
If a new furnace or heat pump is in sight, your best bet is to replace it before heating season as well. You’ll have the benefit of more flexible scheduling with your contractor and have the time to fully research your options, so you don’t feel rushed making a critical decision quick when temperatures are dropping and your family has no heat.
The furnace or air handler’s blower motor and fan responsible for circulating heated air from the furnace, through the ducts, and into your living areas. The motor is linked to the fan via a belt, which allows the motor to rotate the fan.
Over time, belts can wear out, fray, loosen, or even break. During a professional heating system tune-up, the belt is typically inspected and replaced if necessary. However, it’s still a good idea to check this component as you prepare your heating system for cold weather to ensure proper system performance.
\r\n
High-efficiency condensing furnaces have condensate drainage systems that allow the condensation produced through operation to exit the system and the home, preventing water damage and system performance issues. Clogs can also cause moisture buildup in the drain line, creating a risk of freezing in the winter, which may result in complete blockages or damage. Check to make sure the condensate drain system is in good working order prior to heating system to avoid water damage and unexpected heating outages.
After your test runs, open the furnace’s access door and find the drip pan. Connected to the PVC drain line that exits the system, in a horizontally installed furnace, the pan sits below the unit; in a vertically installed furnace, the pan sits below the heat exchangers. Carefully remove the pan and look to see if water remains in the pan or if it has exited the system properly.
This type of furnace produces condensation related to the use of its secondary heat exchanger – a component not found in standard models. A secondary heat exchanger is used to capture more energy for heating from the combustion byproducts produced when fuel is combusted in the furnace. Combustion byproducts move from the primary heat exchanger to the secondary heat exchanger and drop in temperature during this process – gases turn into liquid, producing condensation. In a standard furnace, combustion byproducts aren’t in the system long enough to convert into liquid and are carried out of the system and home via an exhaust flue pipe, requiring no condensate drainage.
If clogs exist in the condensate drainage system, condensation becomes trapped in the system, which can lead to a number of problems. Water may spill out of the system onto the floor surrounding the furnace, which could damage the system as well as flooring and nearby walls. These furnaces are outfitted with float switches (also called overflow switches or wet switches) that shut down the system when water level in the drip pan is too high, indicating a clog or blockage of the drainage system or malfunction with the condensate pump, if applicable.
If your home uses liquid propane (also called LP) or heating oil to power its furnace, it’s always wise to check your fuel reserves before the winter season. If you do not have enough fuel in the tank to make it through the winter, make a plan for refueling now to avoid peak season and emergency delivery charges and wait times, whether that be scheduling a refill now or scheduling it when the tank’s volume drops to a certain point.
On average, propane furnaces consume approximately one gallon of LP per hour of heating. Oil furnaces use between two to five gallons of oil per day, depending on outdoor temperatures. You can keep track of tank volume by checking the gauge on the exterior of the tank regularly. Or, take advantage of new remote monitoring technology that allows you to conveniently manage heating fuel levels. Smart oil gauges provide accurate oil level readings within a few gallons, delivering measurements and alerts directly to your smartphone via app. Remote tank monitoring devices for propane may be offered by dealers and provide easy-access monitoring via an online portal. Other products offer Wi-Fi connectivity, allowing homeowners to check tank readings from their smartphones and other connected devices.
Running out of LP or heating oil in your tank will obviously prevent your furnace from heating the home. Letting these tanks run too low or empty can also create other problems, which can be avoided if you carefully monitor tank volumes and schedule refills accordingly. Leaving tank volume too low can also create issues.
If your propane tank is completely out of fuel, it must be inspected before leaks before it is refilled – this is required by the National Fuel Gas Code. Running out of propane can cause moisture accumulation within the tank, leading to rust – the presence of rust weakens the tank and can reduce the rotten egg odor added to propane, which makes it more difficult to detect leaks. There is a risk of leaks upon refilling if gas valves are left open after the tank runs out, which could lead to a fire or explosion. After the tank has been refilled, the furnace’s pilot light must be restarted before operating the furnace.
If you run out of heating oil, it won’t damage your furnace – but it does result in some inconveniences beyond a lack of heat. When tank volume is low or empty, condensation accumulates on the tank’s interior walls, causing rust and even bacterial growth that can clog oil lines and lower heating efficiency. Before restarting the furnace, fuel lines must be bled to remove air that has been drawn into the system. The oil filter may also need to be cleared or replaced to eliminate sludge.
If you have troubles keeping all areas of your home adequately heated throughout the winter, consider the installation of a zoning system. Zoning is an excellent and energy-efficient way to remedy troublesome hot and cold spots throughout the home while allowing all areas to receive the right amount of heating to meet their individual demands.
Zoning systems separate your home into climate zones – areas with similar construction, use, and other common factors. The heating and cooling system is equipped with a zoning panel, zoning dampers are placed in ducts, and a thermostat is installed for each zone. With this setup, heating in each zone can be controlled using a single furnace, though each area receives differing amount of heat at different times, depending on the comfort demands of the zone.
Zoning systems are helpful in multi-level homes that have a significant temperature disparity between the upper and lower levels. If your second story feels too hot even while those on the lower level are too cold, climate zones help you combat discomfort caused by rising heat and address the unique heating needs of each area within one home. The same thinking applies when trying to heat a basement in winter. Talk to your heating professional about zoning solutions to work with your heating system this winter.
When your home does a better job holding in heat, it minimizes the amount of extra work the heating system must perform to make up for heat loss. Increasing insulation levels throughout attics and under floors enhances energy efficiency, so more of the heat your furnace or heat pump delivers stays inside for the benefit of your family. Insulation can be installed as a DIY project or professionally installed, and there are a variety of insulation products to choose from, including blown insulation and insulation batting available made from various materials.
Consider insulating areas of your home as well as your ducts to improve heating this winter. Cold air contact and infiltration from unconditioned areas causes heat loss in ducts, meaning less heat makes it to your living areas than what was produced by your heating system. Installing insulation for ducts that sit in unconditioned areas can significantly lower heat loss.
Give your heating system some extra help this winter and save energy, too! Adjust ceiling fans to rotate clockwise. There is a switch on the motor casing that allows you to change the rotational direction of the blades.
When fans spin clockwise, this motion creates an updraft in the room that redistributes warm air back down into the spaces of the room that are occupied, allowing occupants to feel more warmth from the home’s heated air instead of allowing it to rise and pool at the ceiling. This effect is only useful when people are present in the room to feel it, so turn ceiling fans off whenever you’re the last one to leave the room to avoid wasting electricity.